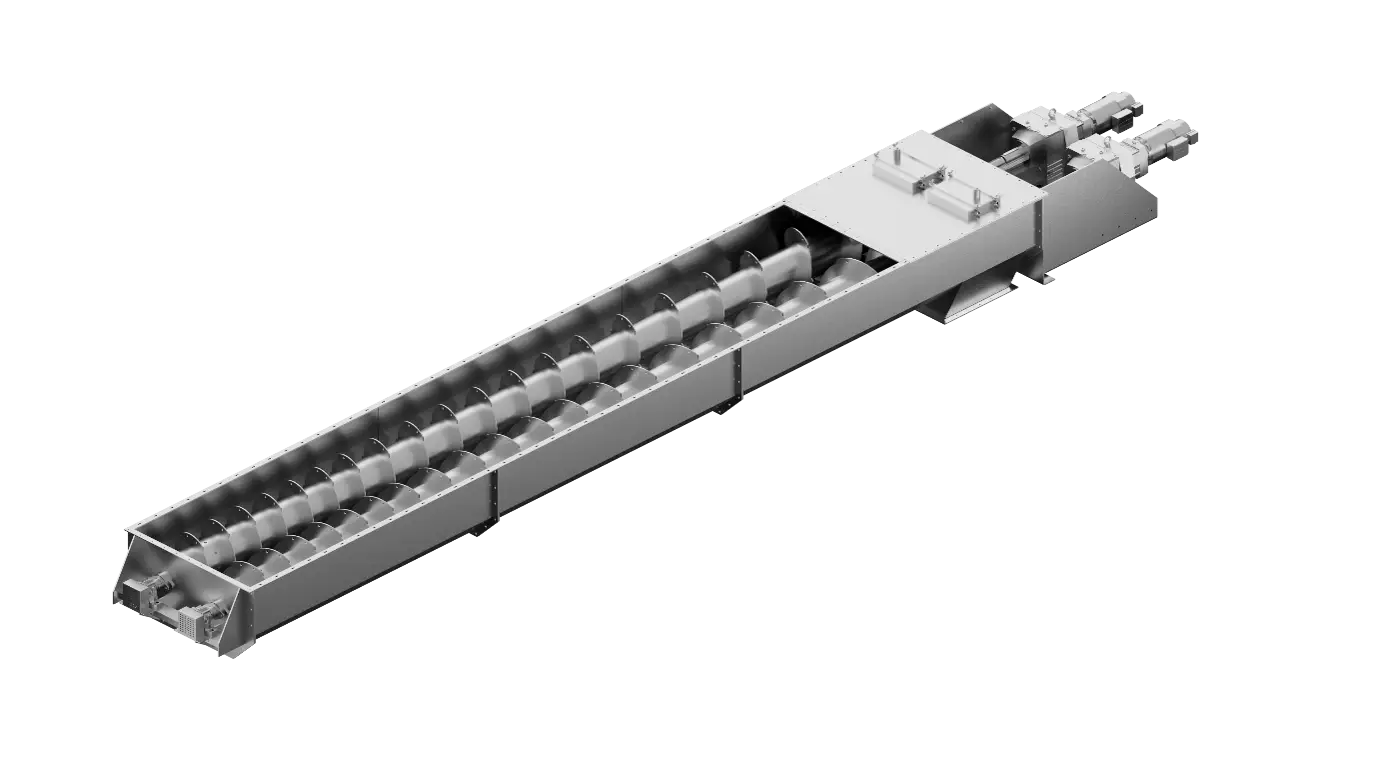
Historia przenośników ślimakowych
Pierwsze wzmianki dotyczące zastosowania rodzaju przenośnika ślimakowego sięgają starożytnej Grecji, kiedy to Archimedes (278 – 212 p.n.e.) zbudował maszynę przeznaczoną do wypompowywania wody z ładowni statku. Wynalazek ten, znany obecnie jako śruba Archimedesa, wykorzystywał zjawisko przemieszczania cieczy za pomocą elementu roboczego w kształcie ślimaka, wówczas wykonanego z drewna oraz napędzanego siłą mięśni. Śruba Archimedesa znalazła zastosowanie także przy nawadnianiu kanałów irygacyjnych.
Przez długie lata nie znaleziono szerszego zastosowania przenośników w przemyśle ze względu na brak potrzeby zapewnienia ciągłego łańcucha transportowego, a także z powodu braku racjonalnego sposobu napędzania urządzenia w inny sposób niż za pomocą siły mięśni zwierząt lub ludzkich rąk. Dopiero pod koniec XVIII wieku konieczność zaspokojenia potrzeb żywnościowych dla rosnącej populacji mieszkańców Ameryki Północnej wymusiła postęp związany z mechanizacją transportu ziaren zbóż.
W roku 1783 Oliver Evans zaprojektował i wykonał linię do transportu mąki wewnątrz młyna, która składała się z przenośników ślimakowych, kubełkowych oraz taśmowych wykonanych z drewna i skórzanych pasów napędzanych poprzez koło wodne. Budowa podajnika ślimakowego była prosta. Pierwsze przenośniki ślimakowe były wykonane całkowicie z drewna. Na okrągłym, drewnianym trzpieniu był zamocowany zespół spiralnych pługów, obracających się wewnątrz drewnianego koryta. Po jakimś czasie Evans udoskonalił konstrukcję ślimaka, tworząc ją z heliakalnie ukształtowanych blach. Odbywało się to w ten sposób, że okrągłe, rozcięte arkusze przypominające spłaszczone pierścienie, były przeciwstawnie naciągane, tworząc kolejne sekcje ślimaka, które z kolei były łączone ze sobą za pomocą nitów. Z czasem drewniany trzpień został zastąpiony stalową rurą.
Kolejnym udoskonaleniem w dziedzinie przenośników ślimakowych był wynalazek zaprojektowany przez Franka C. Caldwella w 1898 roku. Wyeliminował on konieczność łączenia poszczególnych sekcji ślimaka poprzez uformowanie go jako jednolitej wstęgi. Rozwiązanie to jest z powodzeniem wykorzystywane do dziś i nosi nazwę przenośnika ślimakowego bez wału lub ślimaka wstęgowego. Z czasem nitowanie poszczególnych sekcji ślimaków zastąpiono spawaniem w celu zapewnienia gładkiego przejścia pomiędzy łączonymi sekcjami oraz podwyższenia sztywności organu roboczego. Dalszy rozwój technologii zmierzający do usprawnienia konstrukcji i funkcjonalności przenośników ślimakowych ukształtował ich obecną formę oraz znaczenie w mechanizacji i technologii transportu materiałów sypkich.
Zastosowanie przenośników ślimakowych
Współcześnie przenośniki ślimakowe są wykorzystywane w wielu procesach technologicznych, które wymagają mieszania, podgrzewania, chłodzenia, suszenia czy nawilżania materiałów sypkich. Transportują one materiały nie tylko w poziomie, ale także pod kątem lub w pionie. Obecnie sama konstrukcja piór ślimaka jest bardzo zróżnicowana pod względem kształtu. W zależności od potrzeb, ślimaki mogą mieć zmienny skok, stożkową średnicę zewnętrzną oraz wewnętrzną wzdłuż całej długości przenośnika, a ich pióra mogą mieć nieregularny, powycinany kształt.
Również same przenośniki ślimakowe mogą pracować w różnych konfiguracjach. Na jednym wale mogą być montowane pióra o przeciwstawnym kierunku zwojów, jak w tzw. przenośnikach rewersyjnych, stosowanych do dwukierunkowego transportu materiału. W przypadku konieczności zapewnienia bardzo dużych wydajności transportowych stosuje się przenośniki dwu- lub więcej wałowe.
Budowa podajnika ślimakowego
Jak zrobić ślimak z blachy? Obecnie technologia wytwarzania piór ślimaka została mocno usprawniona poprzez ich formowanie w prasach hydraulicznych. Metoda ta pozwala na wytwarzanie ślimaków o bardzo dużym zakresie grubości blach (od 2 mm do 32 mm), dużym skoku (do 800 mm) oraz dużej średnicy zewnętrznej (do 4100 mm), wykonanych z różnych gatunków stali, począwszy od stali węglowych, aż po stale kwasoodporne oraz trudnościeralne. Niezwykle istotną cechą formowania piór w prasach hydraulicznych jest fakt, że cały proces odbywa się bez potrzeby podgrzewania arkuszy blach w celu ich kształtowania. Operacja formowania trwa bardzo krótko i, co najważniejsze, jest zachowana bardzo duża powtarzalność kształtu wytwarzanych segmentów piór.
Rodzaje przenośników ślimakowych
Ze względu na kształt koryta oraz zakres roboczych prędkości obrotowych przenośniki ślimakowe można podzielić na dwa typy. Pierwsze z nich to przenośniki z korytem rurowym, pracujące w zakresie wysokich prędkości obrotowych(od 200 obr/min do 2000 obr/min), które są przeznaczone do transportu suchych i lekkich materiałów sypkich na odległości do kilkunastu metrów. Przenośniki te mogą transportować materiał w poziomie, pod kątem lub pionowo. Podawanie materiału sypkiego do przenośnika ślimakowego rurowego przeważnie odbywa się w sposób ciągły, na przykład poprzez inny przenośnik zasilający.
Drugi typ to przenośniki z korytem o przekroju w kształcie litery U. Pracują one w zakresie prędkości obrotowych nieprzekraczających przeważnie 150 obr/min i mogą transportować materiały kohezyjne oraz gruboziarniste. Zwykle są zasilane poprzez kosze zasypowe, znajdujące się ponad korytem. Inna nazwa tego typu przenośników funkcjonuje jako podajniki ślimakowe.
Niewątpliwie ogromną zaletą podajnika ślimakowego jest prosta budowa urządzenia oraz łatwość dostosowania wydajności masowej poprzez zmianę prędkości obrotowej wału. Zachowanie się materiału sypkiego w trakcie procesu transportu przenośnikiem ślimakowym, jest uwarunkowane szeregiem czynników, związanych między innymi z właściwościami fizycznymi materiału, prędkością obrotową wału, wymiarami ślimaka (średnicą zewnętrzną, skokiem linii śrubowej), stopniem napełnienia koryta czy sposobem podawania materiału do rynny (koryta) przenośnika. Czynniki te w różnym stopniu wpływają na parametry eksploatacyjne przenośnika, czyli na wydajność masową oraz zapotrzebowanie na moc potrzebną do przetransportowania materiału przy zadanej prędkości obrotowej wału ślimaka.
Jako producent przenośników mamy w ofercie ślimaki do podajników dopasowane do różnych potrzeb. Zapraszamy do skorzystania z naszej oferty!